-
-
-
-
-
-
-
-
- Blocked Pitot Tube With Clear Drain Hole
- Blocked Pitot Tube and Drain Hole
- Blocked Static Port
-
- Fix Pitot Tube Blockages
- Fix Static Port Blockages
-
-
-
- Small Errors in the Static Port
- Small Errors in the Pitot Tube
-
-
“Excuse me, sir, do you know how fast you were going? And how high were you flying?” The answers come from a clever little setup on your airplane: a metal tube sticking into the airstream and a tiny hole on the fuselage.
These two simple features power three of the most important cockpit instruments. This setup is called the pitot-static system.
In this article, we’ll break down how the pitot-static system works, what it measures, and why it’s so important.
Key Takeaways
- The pitot-static system measures airspeed, altitude, and vertical speed.
- Blockages in the pitot tube or static port can lead to inaccurate or failed instrument readings.
- Pilots can use pitot heat or alternate static sources to handle blockages in-flight.
- Preflight checks, including removing covers, help prevent blockages caused by dirt, insects, or ice.
What Is the Pitot-Static System?
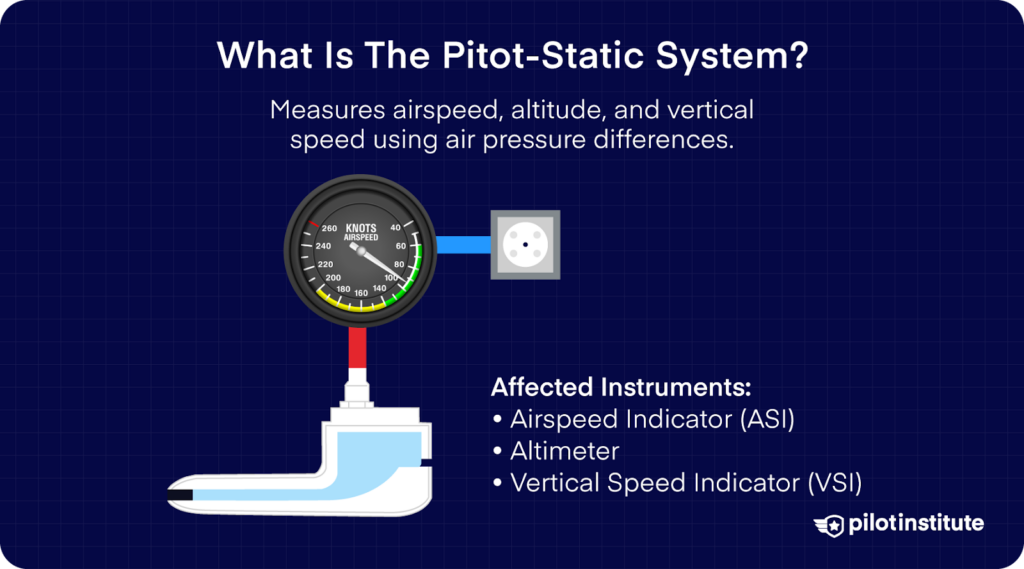
The pitot-static system measures an aircraft’s airspeed, altitude, and vertical speed using air pressure differences.
The respective instruments for showing these readings are:
- The Airspeed Indicator (ASI)
- The Altimeter
- The Vertical Speed Indicator (VSI)
Components of the Pitot-Static System
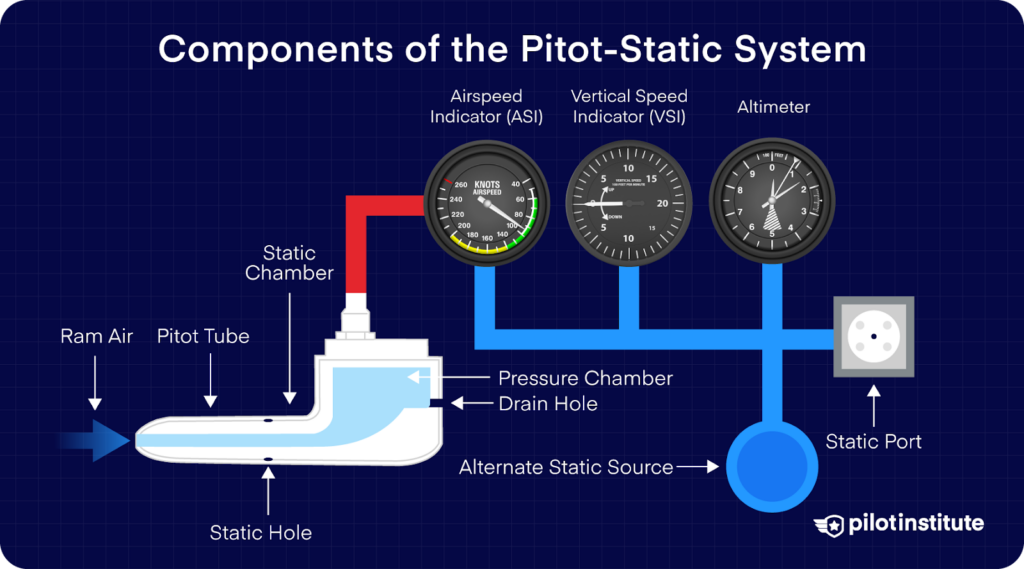
Have you ever noticed the little L-shaped component on the front of an airplane? That’s called a pitot tube.
It helps measure how fast the airplane is going by measuring the air pressure. And do you see that little hole on the back? That’s for draining out any moisture that might get inside.
The other important part of the system is a tiny hole on the side of the airplane, called a static port. This one measures the atmospheric pressure without being affected by the aircraft’s movement.
Both the pitot tube and static port are connected to instruments through tiny pipes that carry the air pressure readings.
If you’re in a modern, fancy airplane with glass primary flight displays instead of round dials, then it uses something called an Air Data Computer to show these readings. Cool, right?
Operating Principle
According to Bernoulli’s Theorem, the total pressure on an airplane stays the same. There are two kinds of pressures that an airplane faces.
One is called dynamic pressure, which happens when the airplane moves through the air. The faster it goes, the stronger this pressure gets.
The second kind is static pressure, caused by the weight of the air above everything. If you fly higher, there’s less air above you and so less static pressure.
When you add these two types of pressure together, you get the total pressure on the airplane.
How Does the System Give Inputs to the ASI?
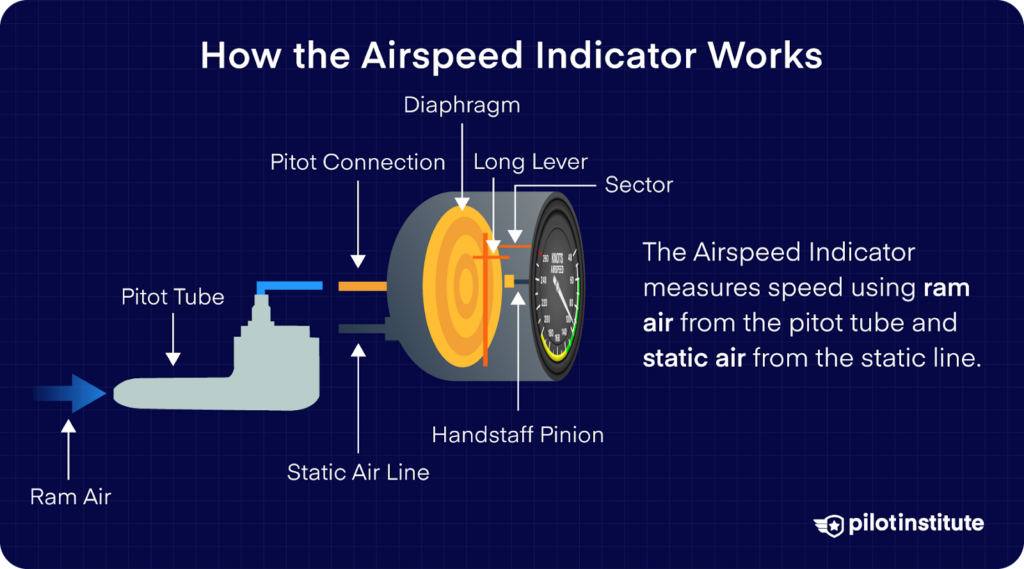
The Airspeed Indicator is the only instrument that uses both the pitot tube and the static port.
As the aircraft moves, air exerts pressure against its motion—this is called dynamic pressure.
The pitot tube, facing the oncoming wind, measures this dynamic pressure along with the static (atmospheric) pressure.
Together, this is called total pressure.
To calculate airspeed accurately, we need to separate the dynamic pressure from the total pressure.
Since static pressure changes with altitude and weather, the static port provides a constant reading of the current atmospheric pressure. This allows the system to subtract it and display the correct airspeed.
The Airspeed Indicator (ASI) uses inputs from both the pitot tube and the static port, separated by a diaphragm.
Static pressure fills the ASI case, while the pitot tube sends total pressure to the diaphragm.
The difference between these pressures creates dynamic pressure, causing the diaphragm to move. This movement drives the ASI needle, showing airspeed.
Some pitot tubes combine static and total pressure internally, sending only dynamic pressure to the ASI for a simpler design.
Remember, the ASI measures airflow relative to the aircraft, so strong wind gusts or turbulence can affect its readings.
How Does the System Give Inputs to the Altimeter?
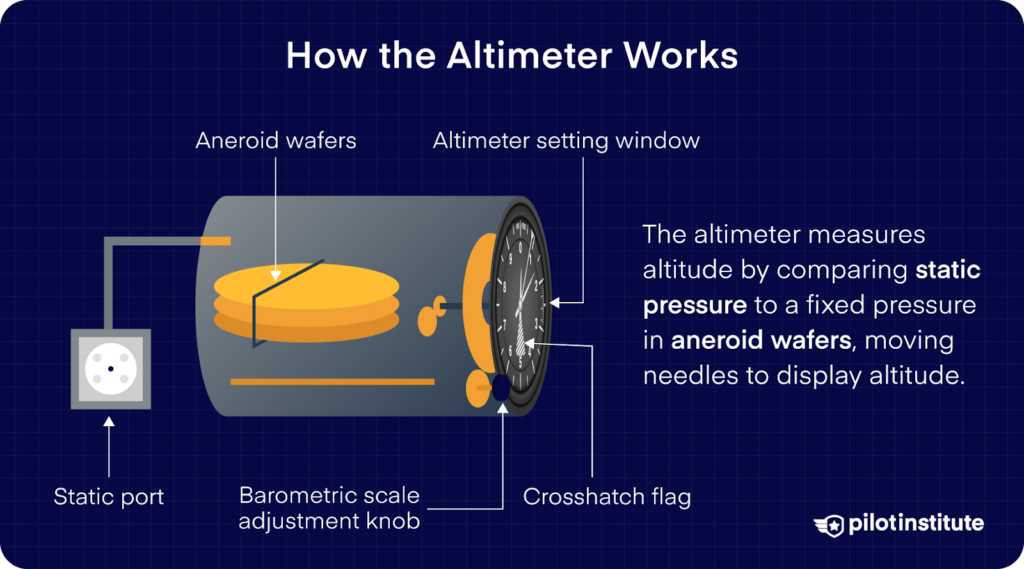
The atmospheric, or static pressure, varies with altitude and weather. The altimeter uses the input from the static port to determine the altitude.
The altimeter is the only instrument in small aircraft that gives the pilot altitude information.
The altimeter measures altitude by comparing static pressure in its sealed chamber to a fixed pressure inside a diaphragm, set at 29.92 inHg (standard sea-level pressure).
As the aircraft climbs and static pressure decreases, the pressure difference moves the diaphragm, which turns the altimeter’s needles.
Since atmospheric pressure changes with weather, pilots must adjust the altimeter using the local barometric pressure shown in the Kollsman Window. If not adjusted, altitude readings may be inaccurate, risking collisions or terrain hazards.
Temperature also affects the altimeter—colder air makes your true altitude lower than indicated, so pilots should account for this, especially over mountains.
How Does The System Give Inputs To The VSI?
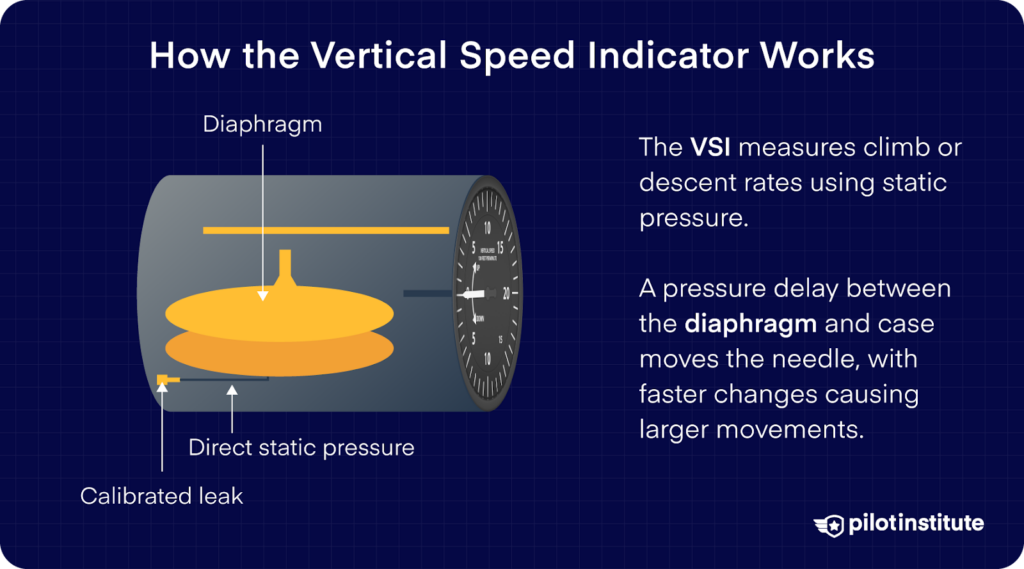
The Vertical Speed Indicator also relies solely on the static pressure input. As the name implies, the VSI shows the rate of the aircraft’s climb or descent.
It shows the rate of climb or descent in feet per minute. When you’re flying at a constant altitude, it should indicate zero if it’s been calibrated properly.
In the VSI’s case, the static pressure enters the instrument through the static pressure line that you can see in the diagram.
This line connects to the inside of the diaphragm. The static line also has a restricted hole that leaks pressure at a calibrated rate to the instrument casing.
Both of the inputs come from the static port, but the inside of the diaphragm has an unrestricted opening, and the VSI case has a metered opening.
When the aircraft climbs or descends, the static pressure will change instantly in the unrestricted opening, but the case pressure will take longer to adjust because of the restricted opening.
This creates differential pressure acting on the diaphragm, which then moves and rotates the connected needle too.
The faster the rate of climb or descent, the greater the differential pressure, and the more the needle will swing.
Blockages In The Pitot-Static System
The pitot tube and static ports are exposed to ice, dirt, moisture, or insects. If they’re blocked, your instruments can give false or no readings. In Instrument Meteorological Conditions (IMC), you must rely on instruments, so knowing how to diagnose these issues is critical.
In 1996, Aeroperu Flight 603 crashed when static ports were taped over, leading to conflicting instrument readings. To avoid pitot-static errors, keep the pitot hole, static port, and drain hole clear.
Blocked Pitot Tube With Clear Drain Hole
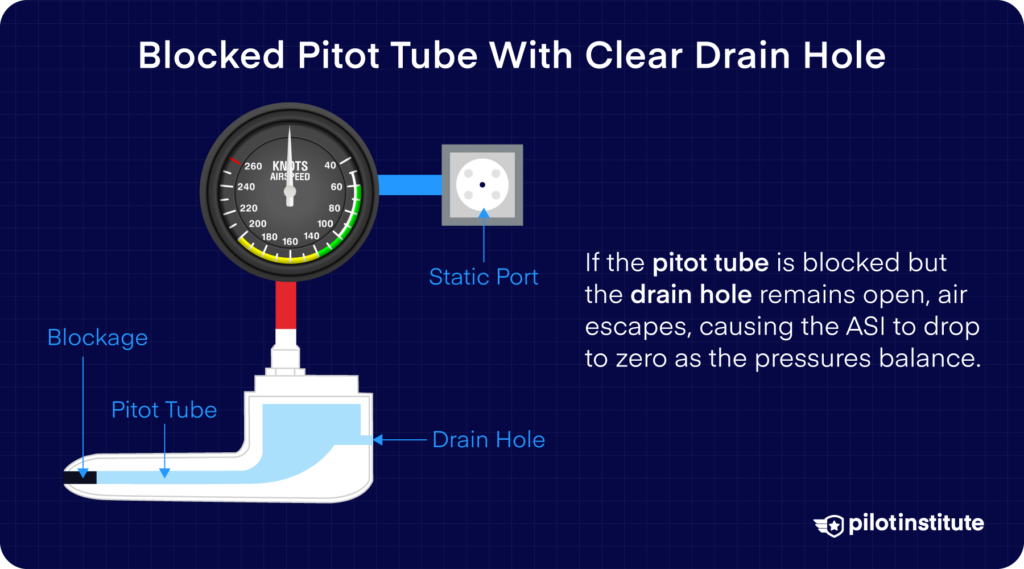
If the pitot tube is blocked but the drain hole stays open, air escapes, and the ASI drops to zero as pressures equalize.
Blocked Pitot Tube and Drain Hole
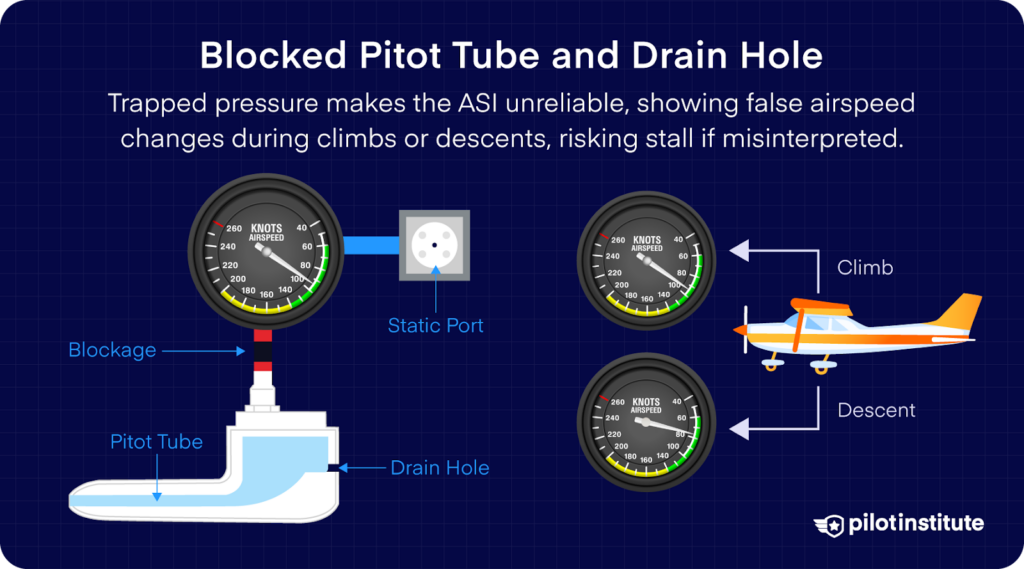
If both are blocked, trapped pressure prevents the ASI from measuring airspeed. At a steady altitude, it will display a constant, unchanging speed.
During a climb, it shows increasing airspeed; during descent, it shows decreasing airspeed, regardless of actual speed. This can mislead you into reducing throttle, risking a stall.
Blocked Static Port
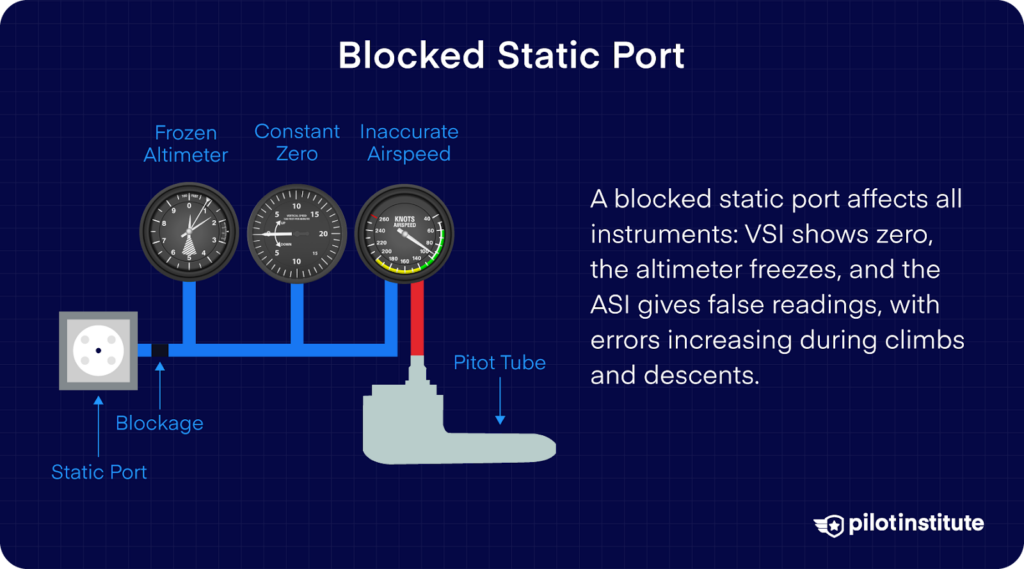
A blocked static port traps pressure, affecting all three instruments. The VSI shows zero, the altimeter freezes, and the ASI gives incorrect readings.
The farther you fly from the blockage altitude, the greater the ASI error—showing higher speeds during descent and lower speeds during climbs
How Do We Fix Failures In Flight?
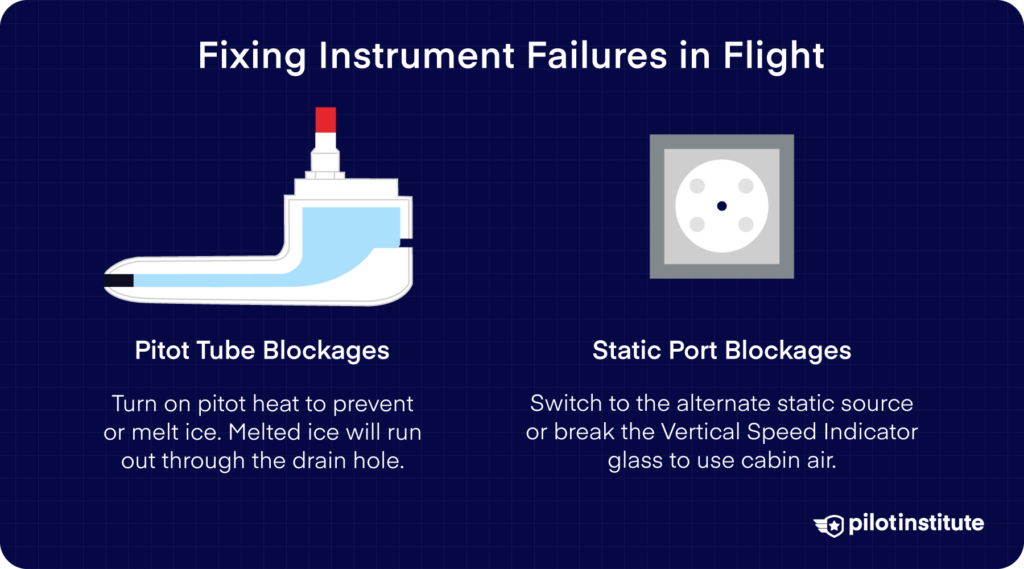
Fix Pitot Tube Blockages
Icing is the most common in-flight blockage, especially for the pitot tube, which faces airflow and has a narrow opening.
If you see moisture, turn on the pitot heat to activate the heating elements and prevent ice buildup. If ice forms, it takes time to melt, draining through the drain hole.
One tragic case was Air France Flight 447, where iced pitot tubes caused faulty readings, leading to a stall and crash.
Fix Static Port Blockages
Static ports rarely ice over, but if they do, use the alternate static source if your aircraft has one. This switches to cabin air pressure, which isn’t as accurate but keeps your instruments working.
If your aircraft lacks an alternate static source, break the glass on a pitot-static instrument to let cabin air into the system. If you must, sacrifice the Vertical Speed Indicator, as it’s the least critical instrument.
How To Prevent Blockages On The Ground?
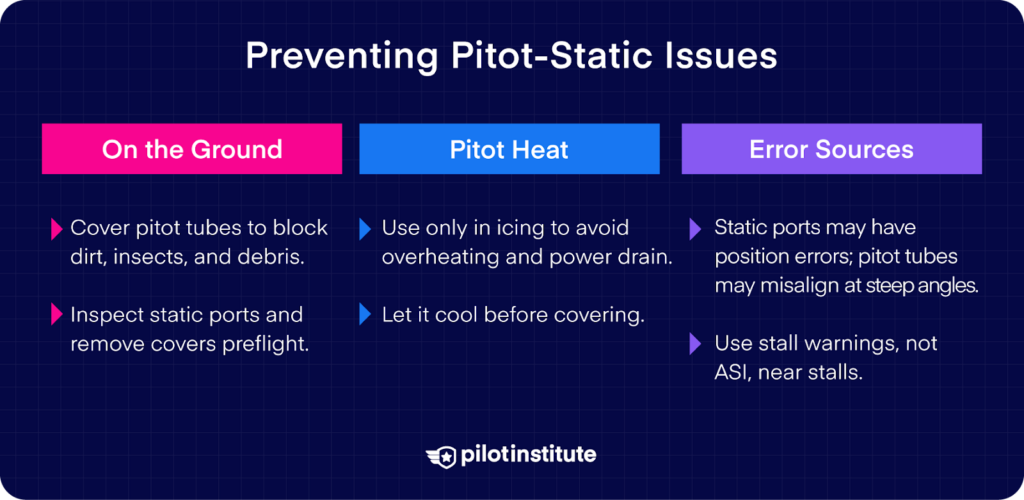
When your aircraft is parked on the tarmac, the pitot-static system faces other risks. Windy conditions over time can increase the chances of blockages from dirt and dust.
Small holes like the pitot tube can attract insects, even for nest-building.
Here’s some perspective of how serious this is: The likely cause of the crash of Birgenair Flight 301, a Boeing 757 carrying 189 people, was a wasp nest built inside the pitot tube.
The aircraft had spent at least two days parked with the pitot tubes uncovered, which was enough time for the wasps to block one of the pitot tubes.
To prevent this, pilots or ground crew cover the pitot tubes with a bright “Remove Before Flight” cover.
On your preflight walkaround, always check that these covers are removed. Forgetting one means losing airspeed information until you land.
Static port blockages are even more critical since they affect all three pitot-static instruments. The Aeroperu crash is a strong reminder to inspect static ports during your walkaround too.
Why Not Have The Pitot Heat On All The Time?
In flight, the surrounding air cools the pitot tube, but on the ground, heat builds up if you leave the pitot heat on. The tube can reach several hundred degrees, which can burn you or melt the cover when securing the aircraft.
Always cover the pitot tube after a flight, but wait until it cools down. Leaving the heat on also wears out the heating elements and adds strain to the electrical system.
In small airplanes, the alternator or generator is the primary source of electrical power during flight. In case of alternator failure, the airplane switches to battery power, which can drain quickly in an emergency. Use pitot heat only when flying in visible moisture at temperatures near or below freezing.
Other Sources Of Errors
The pitot-static system also encounters errors that are less drastic but still fairly significant. A small amount of error is acceptable for normal flight operations, but it’s not practical to completely remove it.
Small Errors in the Static Port
The static port is vulnerable to position errors. Aircraft manufacturers try to place the static port in a position on the fuselage where it can measure the atmospheric pressure without any influence from the aircraft’s movement.
In reality, it’s not possible to have zero position error at all angles of attack the aircraft experiences. Still, the static port is placed in a location where the error is as low as possible.
Small Errors in the Pitot Tube
The pitot tube doesn’t have position error since it measures total pressure, but it does experience alignment error.
If you’re not flying straight and level—like in a bank, sideslip, or steep nose-up or nose-down attitude—the airflow to the pitot tube can be blocked by the fuselage or misaligned with the relative wind.
This reduced airflow lowers dynamic pressure, causing the ASI to show incorrect airspeed. Alignment error usually occurs when the relative wind is angled more than 15 degrees to the pitot tube, such as during a high Angle of Attack before a stall.
In these situations, rely on the stall warning horn, not the ASI, to detect a stall.
How Do We Counter The Small Errors?
You can reduce small errors in the pitot-static system by using static ports on both sides of the fuselage. This balances pressure readings during a bank or side wind. Pitot tubes, on the other hand, typically work independently to provide redundancy.
Larger aircraft often have multiple, independent pitot-static systems—one for the captain, one for the First Officer, and sometimes a third for backup—providing redundancy.
During takeoff, the Pilot Monitoring (PM) calls out airspeed, usually at 80 knots, and the Pilot Flying (PF) verifies it matches their ASI.
Even if your general aviation aircraft has only one system, calling out airspeed on takeoff ensures the pitot tube is working and uncovered.
Conclusion
The Airspeed Indicator, Altimeter, and Vertical Speed Indicator are important tools for any pilot. It’s amazing how such a simple system, powered by air pressure, keeps you informed during flight.
But when something goes wrong, it can get tricky fast. Learning all about how the pitot-static system works—and how it can fail—helps you stay ahead of potential issues.
The more you know, the safer you’ll feel on your next flight.