Your first taste of a complex aircraft system was likely an introduction to the constant-speed propeller.
While a constant-speed propeller system is not too difficult to operate, many pilots do not fully understand how it works, and many do not understand why it exists.
This article will explain what a constant speed propeller is, how it works, and how to use it correctly in the cockpit so that you can use the variable-pitch system with confidence.
Key Takeaways
- Constant-speed props hold RPM by adjusting blade pitch.
- Throttle sets power; prop lever sets RPM.
- The governor uses oil and flyweights to manage pitch.
- Misuse can damage the engine—know how it works.
What Is a Constant-Speed Propeller?
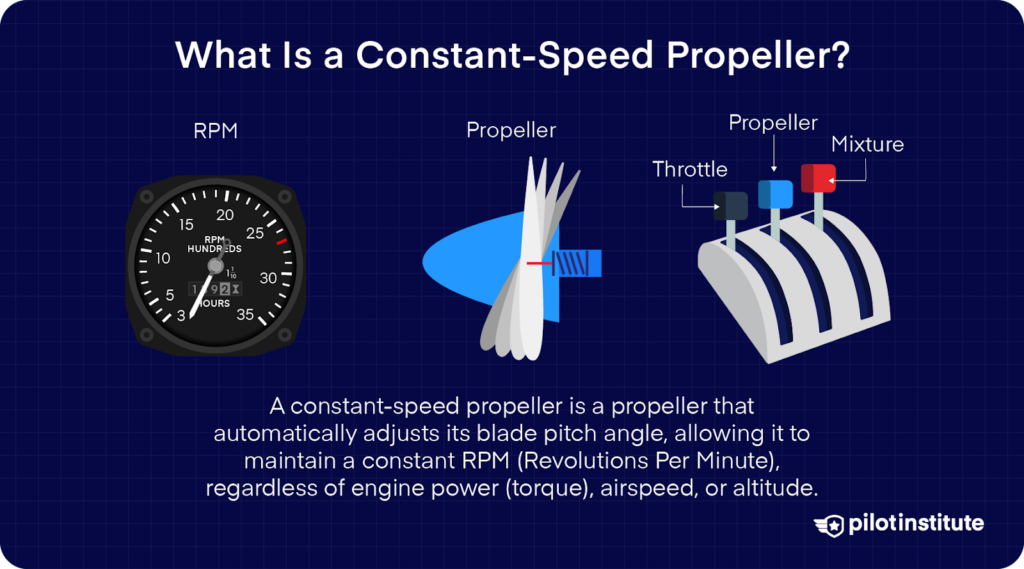
A constant-speed propeller is a propeller that automatically adjusts its blade pitch angle, allowing it to maintain a constant RPM (Revolutions Per Minute), regardless of engine power (torque), airspeed, or altitude.
The constant-speed propeller is often referred to as the variable-pitch propeller, in contrast to the fixed-pitch propeller.
Generally speaking, with a fixed-pitch propeller, optimal efficiency is only obtained at a certain airspeed and power setting. With a variable-pitch (constant speed) propeller, optimal efficiency can be obtained at a wide range of airspeeds and power settings.
A constant-speed propeller is a system that allows turbo-propeller aircraft to operate efficiently within a wide speed range. This allows turbo-propeller aircraft to be used for a variety of missions.
How Does It Work?
The propeller’s pitch angle is controlled by a hydraulic system that uses the aircraft’s engine oil. This hydraulic system is controlled by the use of a blue lever inside the cockpit, referred to as the propeller or pitch lever.
The component that controls this entire system is called the propeller governor or Constant Speed Unit (CSU).
A threaded shaft is connected to the pitch lever, with a speeder spring between the threaded shaft and the flyweights. The flyweights are “L” shaped and are connected to the engine.
The flyweights spin in a circular fashion. The speeder spring is squeezed down as the threaded shaft moves downwards. This causes the flyweights to move inward. If the threaded shaft moves upwards, the speeder spring is released, and the flyweights move outward.
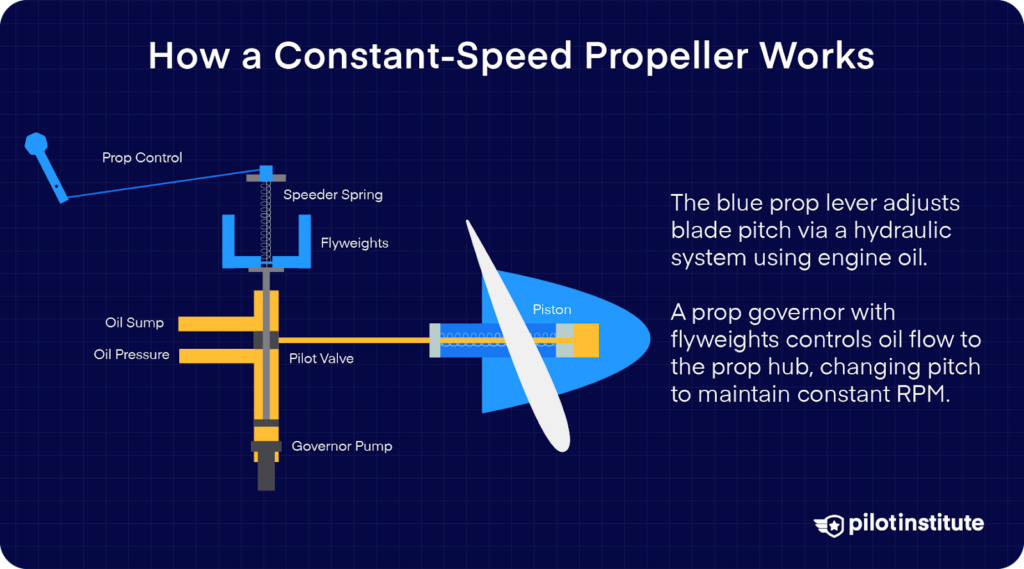
Because the flyweights are connected to the engine, when the engine speed increases, the flyweights spin faster and move outwards due to centrifugal force.
The threaded shaft is connected to a pilot valve, which controls the flow of oil into and out of the propeller hub.
When the flyweights move outwards, the threaded shaft moves and lifts the pilot valve up, allowing oil to enter the propeller hub and thereby changing the pitch angle of the blades.
This also works in reverse: Engine speed decreases, the flyweights spin slower, the flyweights move inwards, the pilot valve moves down, oil is prevented from entering the propeller hub, and the pitch angle of the blades is changed.
A Practical Example
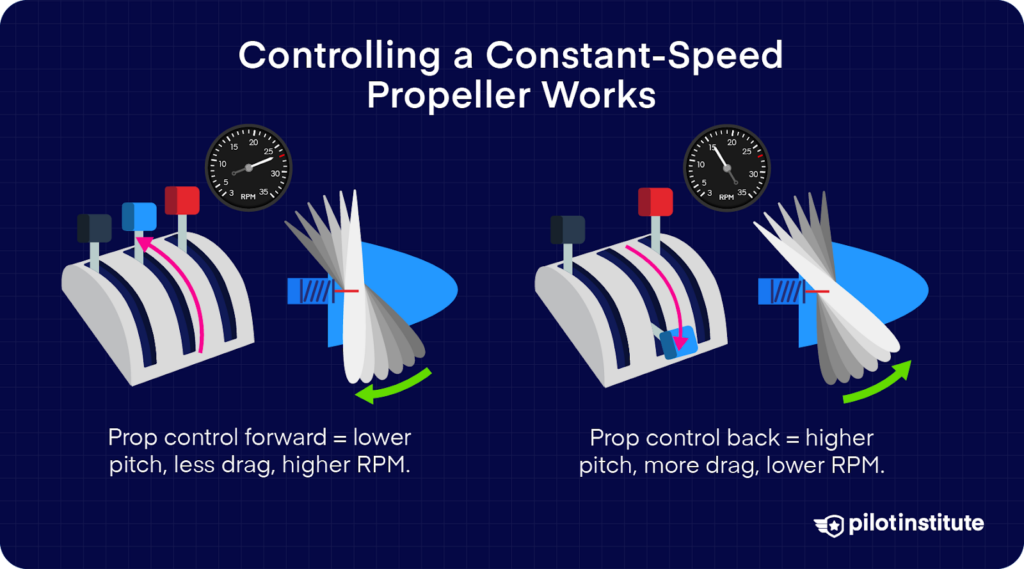
The prop lever (i.e., pitch lever) is placed in the full forward position when taking off and landing. In this case, the propeller is in the high RPM (low pitch angle) setting.
After takeoff, during the climb, this pitch setting is no longer the optimal setting, and the pitch angle (RPM) must be adjusted. The pitch lever must be moved back to reduce RPM to the optimal setting for the climb.
When the pitch lever is moved back, the propeller pitch angle becomes “coarse” (the opposite is called “fine”), and the propeller takes a larger “slice” of air by increasing the blade’s angle of attack.
When the propeller’s angle of attack increases, the engine’s torque increases, which effectively “slows down” the engine’s components. During cruise flight, this increases fuel efficiency and prevents wear on the engine components – akin to changing gears in a car.
Maintaining RPM
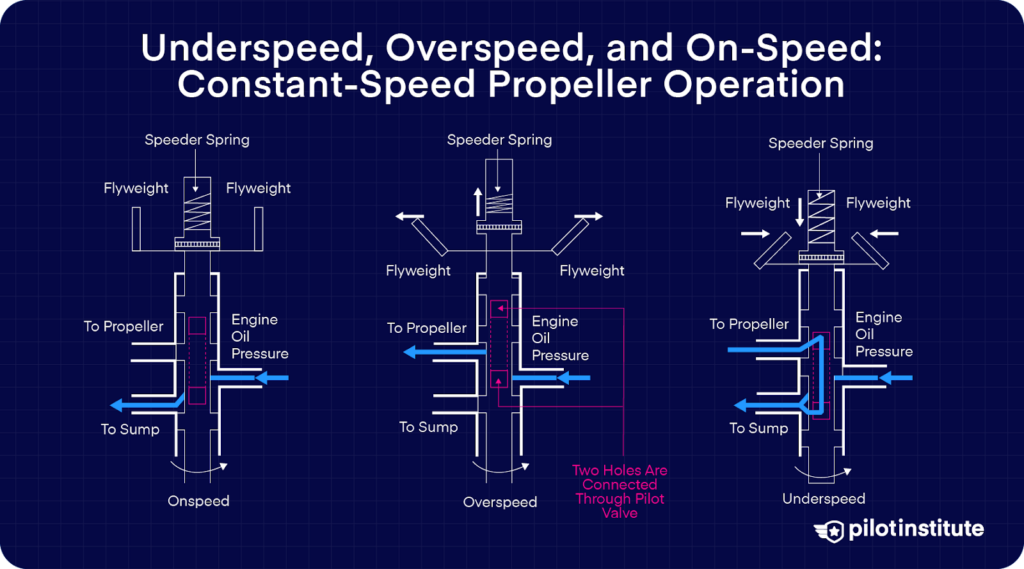
Underspeed
When the RPM drops below the RPM set by the pilot using the pitch lever (when initiating a climb, for example), this is known as an underspeed condition.
To correct an underspeed condition, the flyweights tilt inward due to the reduction in centrifugal force from the decrease in RPM. Due to the tilting of the flyweights, the speeder spring extends, which causes the flyweights to move inward.
The pilot valve is then forced down by the speeder spring, and oil in the piston of the propeller hub is reduced, thereby reducing the blade pitch angle.
As the pitch angle decreases, RPM increases to the RPM initially set by the pilot.
Overspeed
Conversely, when the RPM increases above the RPM set by the pilot using the pitch lever (in descent, for example), this is known as an Overspeed condition.
In an Overspeed condition, the force of the speeder spring cannot overcome the force of the flyweights as they tilt outward due to the increase in centrifugal force.
This moves the pilot valve up, and the oil in the piston of the propeller hub is increased, which increases the blade pitch angle.
On-Speed
When the engine operates at the RPM set by the pilot, this is called an on-speed condition. In an on-speed condition, the flyweights’ centrifugal force and the speeder spring’s force are balanced, causing the pilot valve to remain stationary. Because the pilot valve remains stationary, oil is not moved to or from the piston inside the propeller hub.
What If You Lose Engine Oil?
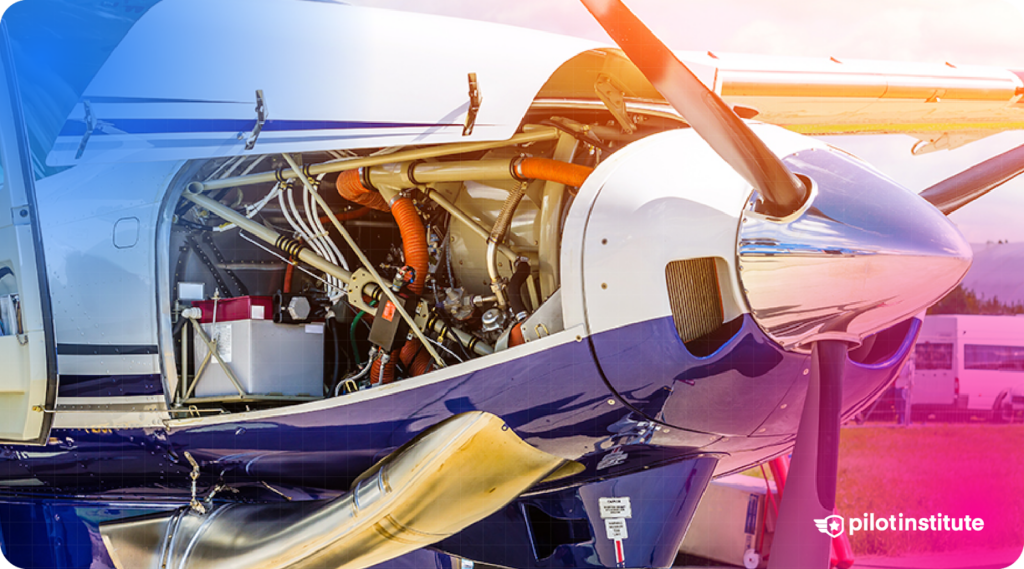
If you lose engine oil, the propellers are designed to move into the high RPM setting (equivalent to the fully forward position of the pitch lever).
This is achieved by the spring of the propeller hub piston, which naturally moves the piston forward (and the propellers in the low-pitch setting) in the absence of engine oil in the piston.
Frequently Asked Questions
- What’s the point of a constant-speed propeller?
A constant-speed propeller lets you choose the most efficient engine RPM for each phase of flight.
The system automatically adjusts blade pitch to hold your selected RPM, so you can get maximum power during takeoff, better climb performance, and improved fuel efficiency during cruise.
- How do you operate an engine equipped with a constant-speed propeller?
You use three primary controls: the throttle, propeller control, and mixture.
The throttle controls manifold pressure (power), the propeller lever sets RPM, and the mixture adjusts fuel-to-air ratio.
For takeoff, you push both the throttle and propeller control full forward. In cruise, you reduce RPM for efficiency, then adjust throttle to match.
When you add power, increase RPM first.
When you reduce power, pull back the throttle first—then lower the RPM.
- What does the throttle do on a constant-speed propeller?
You use the throttle to set engine power by adjusting manifold pressure. The propeller governor takes care of the blade pitch, keeping the RPM constant.
When you increase throttle, manifold pressure rises, and the governor increases blade pitch to keep RPM steady.
- What controls the constant speed range of a constant-speed propeller?
The propeller governor controls the constant-speed range. It senses changes in engine RPM and adjusts oil pressure to change the blade angle.
You set the desired RPM with the propeller control, and the governor keeps it there by changing pitch as needed.
Internal stops limit how far the blades can move, setting the high and low ends of the range.
Conclusion
The variable pitch propeller is a critical component and allows propeller aircraft (particularly turbine aircraft) to be far more efficient.
While the concept of how the flyweights, speeder spring, and pilot valve interact can be difficult to grasp, you must understand how this system functions.
You will likely fly an aircraft with a variable pitch propeller one day, and there is a good chance that you will not operate the system correctly if you do not understand how it works.
Take note; Using the variable-pitch system incorrectly can lead to irreparable and expensive damage to the aircraft’s engine.