- Understanding Friction
- Static and Dynamic Friction
- Changes in µ
- Changes in N
-
- Dynamic Hydroplaning
- Reverted Rubber Hydroplaning
- Viscous Hydroplaning
-
- Going For the Alternate
- Preflight Planning
- Preparation on Approach
- Limiting Speed
- Tire Maintenance
-
-
- Autobrakes
- Anti-Skid Brakes
- Reverse Thrust
- Aerodynamic Braking
-
Hydroplaning, or aquaplaning, is the skidding or slipping of an aircraft tire during takeoff, landing, or taxiing due to the presence of a contaminant on the surface – usually water. It’s one of the most common risk factors for runway excursions and can cause anything from a mild scare for a pilot to a deadly crash.
Understanding Friction
In order to better understand how a tire loses grip, it’s helpful to know how it manages to grip the surface in the first place.
Whenever two objects are in contact with each other and one of them is moving relative to the other, a force will be generated resisting the motion. The magnitude of this frictional force is given by this very simple equation:
F = µ x N
Where F is the frictional force, µ is the coefficient of friction between the two surfaces, and N is the Normal force.
Why does the frictional force exist at all?
It makes sense that if a body hits a surface head-on, like a ball bouncing on the ground; the surface is going to exert a force against the body in return. That’s commonly known thanks to Newton’s Third Law of Motion. But the scenario of the wheel moving along the runway involves a body moving along the surface, not against it. What’s the reason for the countering force here?
In reality, all solid surfaces have at least some irregularities and imperfections that might not be visible to the naked eye but exist at the microscopic level. Rubber, for example, has a surface composed of polymers and elastomers. These have long molecular chains that project outwards and get caught in protrusions coming from the surface it is in contact with.
So while the body as a whole is moving along the surface, some of its projections are banging against the areas of the surface that jut outwards, generating a countering force that resists the movement. That force is the frictional force.
Static and Dynamic Friction
Frictional force can be divided into two types: Static and Dynamic Friction.
Static friction is the force that exists between two objects that are in contact but not moving relative to each other. This force opposes any attempt to create relative motion and is the force that’s the cause of the ‘grip’ that tires have on the runway.
It would be fair to ask why we’re talking about static friction when moving wheels on a surface are involved.
As the wheel rotates over the surface, the patch of the wheel that comes into contact with the surface does not move relative to it. The rest of the wheel rotates around that point of contact. As the static frictional force is preventing relative motion between the patch and the ground, it’s generating a reaction force that propels the wheel forward.
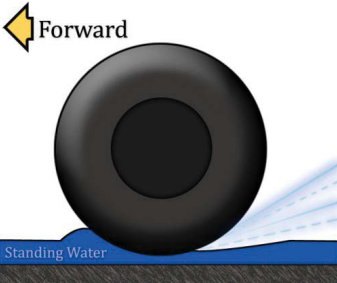
In contrast, if the wheel does not spin, but instead skids over the surface, the contact patch is sliding against the ground. There’s relative motion between the patch and the surface and no static force available to propel the wheel. The force opposing the motion here is the dynamic frictional force. When compared to static frictional force, the dynamic force will always have a lower magnitude. The protrusions in each surface aren’t able to fully interlock as they’re in motion, so don’t need a lot of force to break free. The tire in this scenario does not rotate and is said to be locked up.
The difference in static and dynamic frictional forces is represented in the frictional force equation by µ.
Changes in µ
The frictional coefficient µ (pronounced ‘mu’) is a measure of how much frictional force will be generated based on the material properties of both surfaces. In simpler terms, it can be called roughness. It’s important to note that this µ is a property of the interaction between both surfaces, so it is affected if the roughness of either of the two surfaces changes.
When the runway surface is contaminated, the drainage capabilities of the tire and the runway surface both influence the amount of traction available.
The tire roughness is affected by the type of rubber compounds used in the tire’s composition, and how much wear and tear the surface has experienced. Both these factors influence the rate of deterioration of the tire’s tread pattern. Flat spots caused by tire skids, tension and torsion loads, and impact stresses all eat away at the tire surface.
At the micro level, the protrusions in the rubber surface gradually erode away, resulting in a smooth tire surface that offers less purchase for the runway surface protrusions to grip. On a broader level, the wear decreases the tire tread depth, making it increasingly difficult for even a small depth of water to be effectively expelled from under the wheel.
The ground roughness depends on the texture and material used in the construction of the runway. These large-scale surface properties are called macrotexture. The size of the stones or rocks, the compactness of their packing, and the type of rock used in the construction all affect the grip offered by the runway.
Asphalt runways are cheaper and easier to build compared to concrete runways, but have a smoother surface that offers less traction. Smaller airfields commonly have gravel runways. Gravel has a very rough macrotexture, but the rocks are loosely packed, resulting in the lowest traction of the three.
Changes in N
In the case of the aircraft wheels, N is the downward force exerted by the aircraft on its wheels. When the aircraft is static or taxiing, the Normal force is simply equal to the aircraft’s weight.
There are times, however, when there are other forces acting perpendicular to the ground which may add to or cancel out some of the Normal force.
When the aircraft makes contact with the ground during landing, the force of the impact momentarily adds to the Normal force, increasing the frictional force available to the wheel. The impact force is transient, so the added frictional force is not available throughout the landing roll.
Even so, the added force performs a critical function in the brief moment where it does act. The increased frictional force allows the static wheel to spin up to the aircraft’s speed shortly after it makes contact with the ground. The less time the wheel spends skidding instead of spinning, the quicker it can help the aircraft slow down.
Any force acting in the opposite direction of the weight will decrease N. For an aircraft, the primary force countering the weight is Lift. The aircraft’s close proximity to the ground increases its lift due to the ground effect. Even as the aircraft is rolling down the runway during takeoff or landing, as long as the speed is high enough, the lifting surfaces are exerting a significant amount of force acting against the weight.
This is one of the reasons why large aircraft deploy ground spoilers as soon as possible after touchdown. At the moment of touchdown, the aircraft has slowed down enough that it has just the borderline amount of lift to remain airborne. Ground spoilers immediately shave off much of the wing’s lift, dropping the aircraft firmly onto its wheels.
Other variations in N appear if the runway is not perfectly flat. While airport planners do try to make runways as flat as possible, most runways have undulations along the strip’s length. Encountering an upslope momentarily increases N, making the aircraft stick to the runway.
Transitions to downslopes are more dangerous since the temporary decrease in N increases the chances of losing grip. Variations in N due to crests or troughs along the runway are usually minor factors since the slopes are so gentle.
But for a wheel already close to the limit, an unexpected gradient change coming at an unlucky moment could be the reason for pushing a wheel over the limit into a skid.
Types of Hydroplaning
While hydroplaning just refers to the wheel breaking traction with the runway due to a contaminant and entering a skid, there are multiple types of hydroplaning that end up with the wheel losing grip. These types differ in terms of the conditions that induce traction loss, and the actions needed to counter them. The diagram shows the three main types of hydroplaning that pose a threat to aircraft.
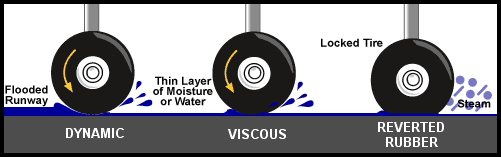
Dynamic Hydroplaning
Dynamic hydroplaning occurs when a layer of water builds up between the tire and the runway surface. This can happen when there’s standing water on the runway or if the aircraft is attempting to land or take off in heavy rainfall.
Like car tires, aircraft tires also have grooves in the surface called tread. Tread channels the flow of water and allows the tire to retain at least some grip on the ground. As the speed of the aircraft increases, a layer of water accumulates under the tire faster than it can be displaced by the tread.
This water pushes back against the tire until eventually, its pressure equals the aircraft’s weight. At this point, the tire completely loses contact with the runway surface and the aircraft effectively “floats” on the layer of water. Since the tire isn’t gripping the runway at all, the pilot no longer has any directional control and the aircraft is left with only ten percent braking capability compared to landing on a dry runway.
For this type of hydroplaning to be possible, the depth of standing water on the runway needs to be at least three millimeters. It can also occur when the contamination is a mixture of water and wet snow.
Dynamic hydroplaning can only happen if the aircraft is traveling fast enough to generate enough water pressure against the motion. The speed at which the tire loses contact is called the Hydroplaning speed (Vp).
Vp depends primarily on the pressure to which the aircraft’s tires are inflated.
Research performed by NASA and the FAA in the early 1960s lay much of the groundwork for guidelines used by the aviation industry to predict dynamic hydroplaning even today. The NASA study proposed what’s now known as Horne’s formula to predict the minimum speed at which an aircraft wheel can experience dynamic hydroplaning, Vp.
Vp = 9 √ P
P in this equation is the aircraft tire inflation pressure, expressed in pounds per square inch (psi). Manufacturer-recommended tire pressure values are easily available for every aircraft. They can be looked up in the aircraft operating handbook or flight manual. Some aircraft even have the recommended value painted on the wheel strut or the landing gear doors.
While the original formula set the value of the constant as 9, a more conservative approach is to use values as low as 6, This modification takes into account the different construction of modern tires as compared to those commonly used in the days when the NASA experiments took place. Modern radial tires deform differently than standard-bias tires, which means they can skid at lower speeds than what Horne’s formula predicts.
Another thing to keep in mind is that the value of Vp is only relevant for the start of dynamic hydroplaning. Once the wheel has started skidding, its interaction with the runway transitions from static to dynamic friction. It will keep skidding even after the aircraft decelerates past Vp and the loss of grip can persist down to very low speeds.
Reverted Rubber Hydroplaning
Reverted rubber hydroplaning happens when heavy braking applied by the pilot locks up the wheels and forces the aircraft into a prolonged skid along the runway. The heat generated due to friction temporarily reverts the rubber into its original, less elastic state, hence the name. If it gets hot enough, the rubber can melt and stick to the runway surface instead.
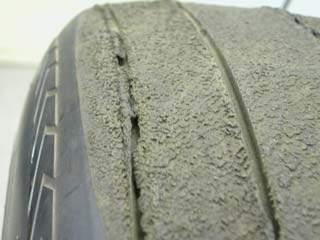
If there’s even a thin layer of water on the runway, the high temperature instantly converts it to steam which helps push the tire off the runway. To make things worse, the reverted rubber layer can get thick enough to block out any water that the tire tread might be trying to evacuate.
Viscous Hydroplaning
Hydroplaning can still happen even if the aircraft has slowed down past Vp, the depth of standing water is less than three millimeters, and Reverted Rubber Hydroplaning hasn’t occurred. The third type of hydroplaning relies on the viscous properties of water and can happen with a layer of water as thin as one-thousandth of an inch. This is called viscous hydroplaning and is also known as film or shear hydroplaning.
The high viscosity of the layer means that the water resists flow. As the tire rolls over the water film, the shear forces between the tread and the water are not strong enough to displace the water or break the film. The only route left for the tire is to float on top of the layer.
Viscous hydroplaning does not have a predictable minimum speed like dynamic hydroplaning, but it can happen at lower speeds than the other two types of hydroplaning. Somewhat counterintuitively, you’re more protected from encountering this type of hydroplaning if there’s more water accumulated on the runway.
The viscous effects are countered by hydrodynamic effects at greater depths of water, basically creating a wave ahead of the tire that breaks the film. Viscous hydroplaning also requires a smooth runway surface such as asphalt, so it’s safer to select a concrete or a grooved runway if there’s one available when landing in these conditions.
Prevention Techniques
Going For the Alternate
Most of the factors described earlier are out of the pilot’s control. The absolute safest course of action is to avoid getting into the situation in the first place; hold until the surface conditions get better or divert to an alternate airfield and live to fly another day.
This isn’t as facetious a remark as it may sound when you first read it. In June 1999, an American Airlines MD-82 slid off the runway at Little Rock, Arkansas while attempting to land at night amidst wind and rain. The NTSB found out that the aircraft overran the runway because of the pilots’ failure to arm the ground spoilers before landing.
While that lapse was clearly due to the stress brought on by the tough landing environment, the NTSB questioned why the pilots even attempted to land in such poor conditions in the first place. One of the contributing factors was described by the lead NTSB investigator as ‘Get-there-itis’. This is a form of bias in the pilot’s decision-making process and is formally known as Task Completion Bias.
When faced with the decision to continue with the landing or abort, pilots may attempt landing even in unreasonably high-risk conditions if they’re at the end of a long, tiring day or otherwise have the incentive to land at the original destination. In the case of American Flight 1420, the pilots wanted to avoid breaching their duty hour limits and so did not want to divert to their alternate airfield.
At least some element of risk is always involved when aircraft are concerned, and it’s up to the pilot as a trained professional to assess the risk.
Preflight Planning
The first decision to prevent hydroplaning is made long before the aircraft even leaves the ground.
According to the FAA CFR regulations for Part 121 and Part 135 flying, pilots attempting to land a turbine-powered transport category aircraft must select a runway that allows the landing roll to be completed within sixty percent of the effective runway length. Pilots compare the landing data provided by the manufacturer in the AFM or POH with the published runway length for the runway and verify that the aircraft will have enough room to come to a stop.
But when pilots plan to land on a contaminated runway, they need to add safety factors to account for the increased risk of hydroplaning. Most POH and AFMs have landing distances published for wet runways as well. For aircraft that don’t have published wet landing distances, the FAA recommends adding fifteen percent to the dry landing distance instead.
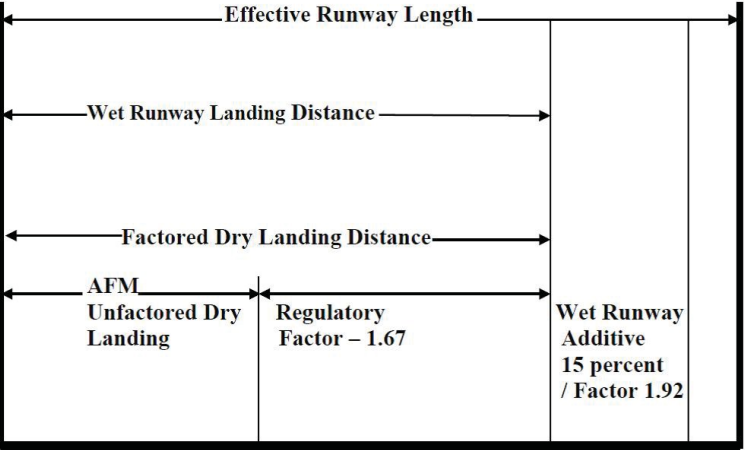
During the flight planning stage, the pilot checks the weather and any NOTAMs valid for the destination airport at the expected arrival time. Special types of NOTAMs called FICO NOTAMs give out runway contamination information. The FAA offers a database that can be searched for active NOTAMs. Indications of rain or snow should alert the pilot to use the landing distances published for contaminated runways.
Runway design has also developed over time to include built-in safety features that reduce the chances of hydroplaning. Runways are constructed with a crowned surface or a transverse slope that drains water out to the sides and away from the tire contact area.
A secondary method of drainage involves cutting grooves into the runway surface perpendicular to the centerline. These grooves channel water away from the center and also help break up the film of water that causes viscous hydroplaning.
When considering an approach to the airport, pilots can reduce the risk of hydroplaning by selecting a grooved runway.
Preparation on Approach
When you’re in the vicinity of the destination airport and tune into the ATIS, the broadcast will mention “braking action advisories are in effect” if the weather conditions are rapidly changing or if poor braking action has been reported by other pilots. ATC will pass on the latest braking action report as you’re coming in for your approach.
Using Braking Action Reports
Why are braking action reports important? Wouldn’t you apply maximum braking every time?
If you’re counting on maximum braking to bring you to a stop before the runway ends, you are effectively cutting the safety margin down to zero. Any contamination on the runway will result in your aircraft’s wheels locking up as they lose traction. As the wheels stop spinning, the friction equation switches from the static friction coefficient to the dynamic friction coefficient. As mentioned earlier, this decreases the frictional force. The massive reduction in available frictional force increases the landing roll, and the lack of a safety margin practically guarantees a runway excursion.
Checking Crosswind Limits
The other effect braking action limits have on the pilot’s decision to land is that they reduce the aircraft’s maximum crosswind limits for landing. When you’re landing in a crosswind, the aircraft approaches the runway with the nose crabbing into the wind. Just before the wheels touch the runway, the pilot realigns the nose with the runway using the rudder so that the wheels don’t skid at the moment of touchdown.
The sideways forces continue to act on the large vertical surface offered by the aircraft’s tail and try to rotate the aircraft’s nose into the wind. All of these forces exert lateral loads on the tires. Once again, if the force on the tires exceeds the available frictional force, the tire loses grip and the aircraft starts skidding. Since the loss of grip is in the lateral direction this time, the aircraft rotates about the vertical axis and is likely to spin out and exit the runway from the side.
Aircraft manufacturers determine the maximum crosswind limits based on the aircraft’s design and performance capabilities. These limits are further tightened for contaminated runways due to the reduced frictional force available to the tires. Pilots need to keep these limitations in mind while looking at the expected weather conditions for their destinations and should make sure they’re still within limits as ATC offers them the latest wind conditions while on their approach.
These limitations are found in every aircraft’s Flight Manual or POH and should preferably be committed to the pilot’s memory as well. Some aircraft don’t have hard limits published by the manufacturer, which offers a maximum ‘demonstrated’ crosswind component instead.
The braking action reports have specific criteria defined by the FAA and shown in the table below. The FAA calls this the Runway Condition Assessment Matrix (RCAM). Pilots describe the braking action as good, good to medium, medium, medium to poor, poor, and nil. The conditions can vary over the length of the runway, so pilots are encouraged to specify troublesome areas in particular.
ATC also takes input from airport operator assessments, shown on the unshaded half of the table. The braking action reports passed on to the pilots on approach make use of both sources of information to give the pilots as comprehensive a picture of the conditions as possible.
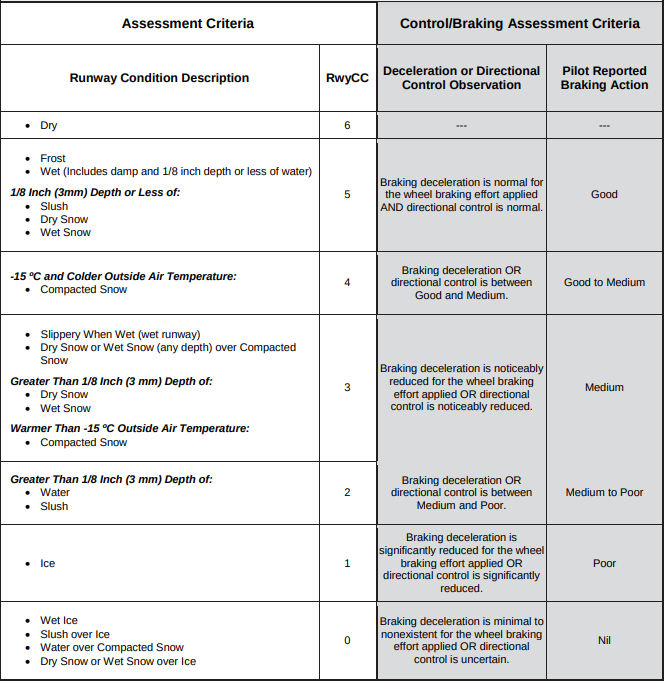
Limiting Speed
One of the most effective ways to prevent aircraft hydroplaning is to reduce your speed. Remember, dynamic hydroplaning can only happen above Vp. Most aircraft have their Vp fairly close to their normal touchdown speed. For example, a Cessna 172 has a Vp of around 40 to 50 Knots depending on the variant. Its normal touchdown speed is around 60 knots.
There’s a small window at the start of the landing roll where the aircraft will be vulnerable to dynamic hydroplaning. The pilot can try to reduce that window by delaying touchdown until the speed decays. The 172’s stall speed is listed at 53 knots in clean and 48 knots in landing configuration, so while you can try to minimize the window, it’s unlikely you’ll be able to eliminate it entirely. The diagram below shows some more examples of light business jets. Note the presence of the ‘window’ in each case.
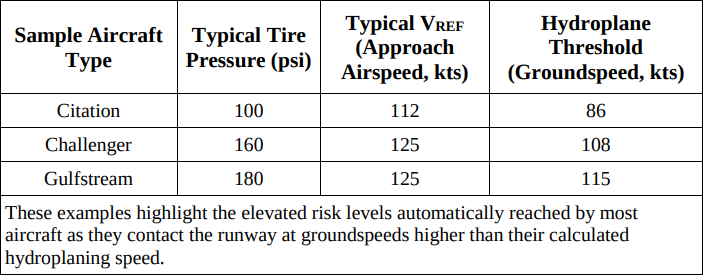
Another thing to think about is that wet runways often coincide with high wind conditions. Gusty winds in particular pose a significant danger to the aircraft when it is in its most vulnerable state: operating with low power and close to the ground. In those conditions, the safer approach is to come in to land at a higher airspeed.
The FAA recommends adding up to half of the prevailing gust factor to reduce the chances of a stall in case the wind drops at the wrong moment. Given how dangerous a low-altitude stall is, it’s better to keep the speed up in gusty conditions and accept the higher risk of some hydroplaning.
Tire Maintenance
Horne’s formula shows that dynamic hydroplaning is all about tire pressure. It’s easy to see that Vp will decrease if the tire is under-inflated. A lower Vp increases the window where dynamic hydroplaning is possible.
Why does low tire pressure decrease Vp?
When a tire is underinflated, the portion of the tire in contact with the ground called the contact patch, is larger and flatter. The changed shape of the contact patch blocks the tire tread from being able to evacuate water effectively. With nowhere for the water to go, the accumulation increases the force acting against the aircraft’s weight and pushes the tire clear off the surface. The flat contact patch helps with this since the wheel has more area to distribute the aircraft’s weight. Increased area means there’s less pressure acting against the water, so the wheel can be lifted up more easily.
Overinflation is not good for the tire either. It causes the center part of the tire to bulge outwards, decreasing the contact patch. This means there’s less tire tread available to channel water away and maintain traction. Overinflated tires also have a reduced ability to deform and conform to the surface of the runway, with the same result.
This is why it is vital to maintain the tire inflation levels specified by the manufacturer, and is the reason a thorough tire inspection is required during the preflight walkaround.
How Would You Know If You’re Hydroplaning?
Detecting hydroplaning can be challenging since the onset is often very subtle. Experienced pilots know the conditions where hydroplaning is likely and actively look out for telltale signs when they see visible standing water on the runway or get reports from other pilots or ATC.
The most obvious early sign of hydroplaning is if the aircraft loses directional control immediately upon touchdown. This is most likely to happen in crosswind conditions where the pilot is attempting to recover from the crab angle.
If there are no detectable steering difficulties, the next indication can be seen on the Airspeed Display. Pilots familiar with their aircraft will be able to tell if it is not decelerating normally. As braking is applied, pilots may get feedback on their brakes from the anti-skid system (if equipped) as it releases the brakes following a skid. The system will release the brakes for longer intervals as the braking difficulties increase.
If the pilot is able to see the aircraft wheels, the presence of lifting spray in the shape of ‘rooster tails’ could indicate that the tires are not effectively displacing water. A sudden whooshing sound from the wheels is also a signal for high chances of dynamic hydroplaning.
Landing and Braking Techniques
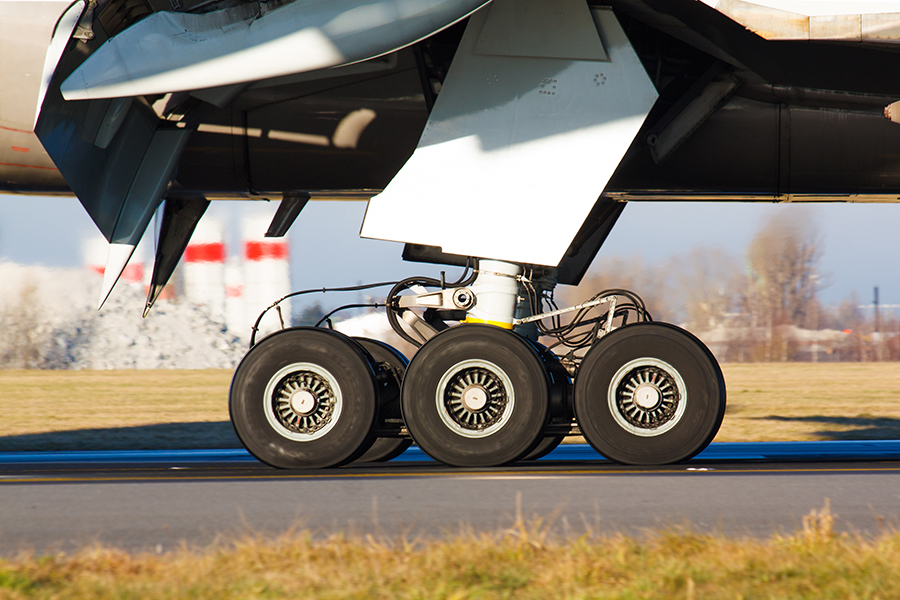
There are some techniques that pilots can use during the flare, touchdown, and landing roll to improve their chances when facing hydroplaning conditions.
Both the FAA and aircraft operators stress the importance of a firm touchdown when landing on a contaminated runway. This isn’t the time to be impressing passengers or worrying about their comfort. A positive touchdown significantly reduces the chances of dynamic or viscous hydroplaning. At the point of contact with the ground, the wheels need to spin up to speed in an instant. Firm landings ensure the wheel breaks through the layer of water and grips the runway.
An additional factor involves the aircraft ground spoilers. If equipped, they use the weight-on-wheel sensors to trigger their automatic deployment. Gentle touchdowns may not trip the sensor at all. Spoilers increase drag by fifty to sixty percent directly, but their more critical function is to transfer the aircraft’s weight from the wings to the wheels. The frictional force equation shows you how important the Normal force is for effective braking action.
Autobrakes
If the aircraft is equipped with auto brakes, pilots should use them whenever hydroplaning conditions are expected. In some aircraft such as the MD-80 series, auto brakes rely on throttle position and ground spoiler deployment. Others such as the 737 use data from the weight on wheels sensor along with wheel speed sensors to activate the auto brakes.
Autobrakes provide predefined deceleration rates with selectable levels of intensity, so are recommended for these conditions by operators and manufacturers alike. The pilot is always able to disarm them by initiating manual braking anytime in the landing roll. Pilots need to ensure the auto brakes have indeed activated during the landing roll and should be prepared to use manual braking in case they haven’t.
Anti-Skid Brakes
If you’ve got Autobrakes on your aircraft, you’ve got Anti-skid as well, since the auto brakes need anti-skid in order to function. The braking technique for aircraft equipped with anti-skid brakes involves applying firm, and if needed, maximum braking pressure throughout the landing roll.
Whenever the wheels start to lock up, the system will release the brakes momentarily and re-engage when the wheel finds grip again. The anti-skid system reacts much quicker than the pilots are physically able to, so they should keep the brake pressure applied and not attempt to release the brakes manually.
Small general aviation aircraft are not equipped with anti-skid brakes although third-party upgrades are available for aircraft like the Beechcraft B200. Pilots braking manually need to apply pressure progressively and manually back off as soon as they notice skidding.
Reverse Thrust
When braking action is limited, reverse thrust from the aircraft engines (if equipped) provides most of the deceleration force. The FAA recommends applying significant reverse thrust only after the nosewheel is in contact with the runway so that the pilot is able to maintain directional control if one of the thrust reversers fails.
If the available runway length is short, maximum reverse thrust can be applied for longer than normal although it comes at the risk of foreign object or water ingestion. Reverse thrust can also hinder directional control if the aircraft is skidding laterally. The best course of action, in that case, is to bring the engines down to idle reverse. This is a tricky set of circumstances with events happening in rapid succession, so the pilot’s judgment ends up being the best tool to keep the aircraft on the tarmac.
Aerodynamic Braking
If the aircraft is not equipped with reverse thrust, the pilot can try to compensate by pulling back on the yoke to transfer as much weight to the main wheels as possible. While doing this maneuver, care must be taken to ensure the nosewheel doesn’t break contact with the ground. Aerodynamic braking can also help but is largely limited to early in the landing roll while the aircraft is still moving at a high speed.
If all else fails, initiate a go-around and attempt to land on a different runway or at a different airport.
The Pilot’s Role in Hydroplaning
Is aircraft hydroplaning considered a pilot error?
Aircraft hydroplaning in itself is generally not considered a pilot error. Hydroplaning can occur due to a number of factors outside of the pilot’s control such as unexpected runway contamination or rapid changes in weather conditions.
However, if a pilot fails to take proper precautions to prevent hydroplaning or fails to follow established procedures for responding to a hydroplaning event, the pilot may be considered to have contributed to the hydroplaning event and could be held responsible for any resulting damage or injury.
It is therefore important for pilots to receive proper training in recognizing the signs of hydroplaning and responding appropriately to prevent accidents. Pilots must have a thorough understanding of the physics involved in aircraft hydroplaning and how to detect and respond to hydroplaning conditions.