Turbine engines have completely revolutionized the aviation industry. They offer unparalleled efficiency and power for modern flight.
But despite their advanced engineering, turbine engines are not without their challenges. Especially when it comes to starting. The ability to identify a failed start and contain the engine is a critical skill every turbine pilot should have.
In this article, we’ll explain exactly how these failed starts can happen, the different types, and how you can identify and contain them.
Types of Failed Starts
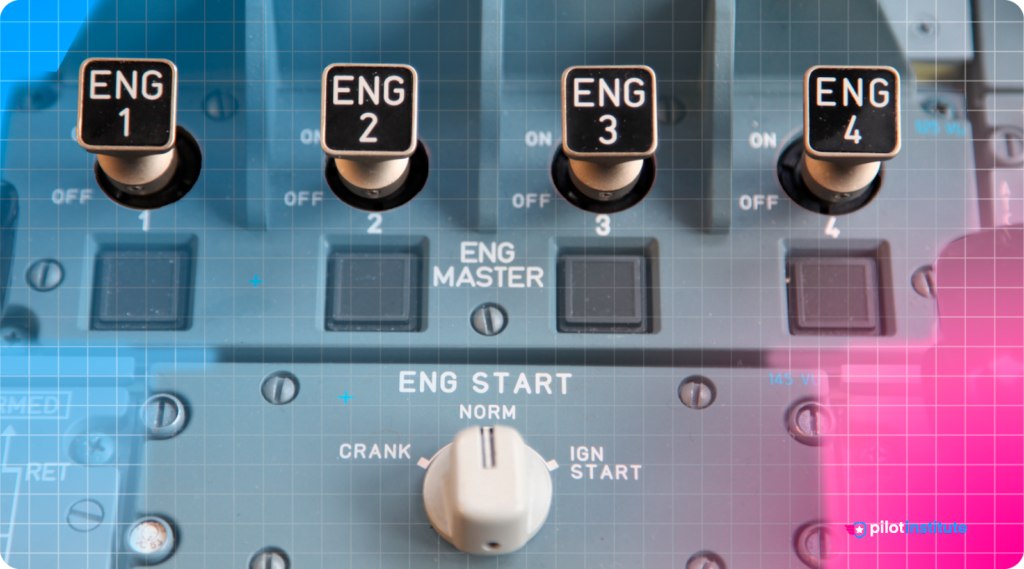
Most modern aircraft have automated starting systems. These systems protect the engine and help assist the pilot, making the process safer. But that doesn’t mean things can’t go wrong.
Let’s have a look at some of the potential problems you may encounter when starting a turbine.
Hot Start
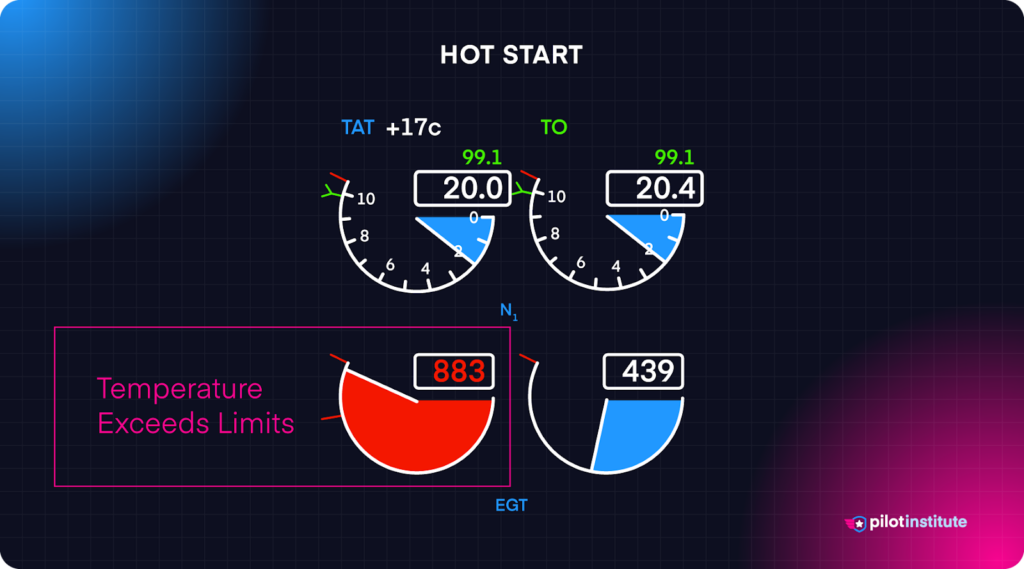
A hot start occurs when the engine’s internal temperature exceeds safe limits. This is often due to excessive fuel flow or insufficient airflow during a start.
A weak starter motor can cause inefficient airflow. Lower currents don’t provide the starter with enough energy. In turn, this causes a high temperature due to limited airflow.
The other cause of a hot start, excessive fuel flow, can occur if the power lever is out of idle.
The only way to stop this temperature exceedance from damaging the motor is to cut off the fuel supply.
Hung Start
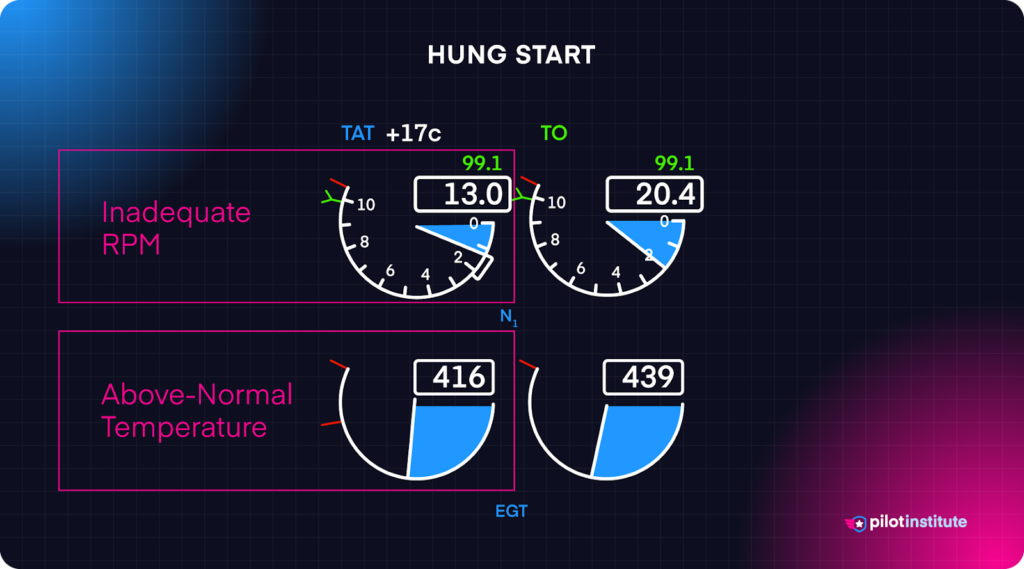
Hung starts occur when the engine fails to accelerate to an appropriate idle speed. Usually stalling at a lower RPM. This is caused by inadequate fuel supply or airflow issues.
Temperatures are usually higher than normal during a hung start due to the lack of airflow and inefficient combustion. During a hung start, there isn’t enough energy to speed up the compressor.
The starter motor then cuts out after it believes its work is complete, leaving the RPM much lower than required and causing a ‘hung’ start.
Pilots will then be unable to go from IDLE to FLIGHT due to the lack of power, and will have to cut the fuel to the engine and try again.
Wet Start

A wet start can happen when the engine receives fuel but fails to ignite it. This can lead to a dangerous accumulation of unburned fuel in the engine. You can see this on the EGT (Exhaust Gas Temperature) gauge, showing no rise in temperature.
If the fuel were to ignite, it would create a small explosion that could severely damage the engine.
Common practice is to crank or “motor” the engine, which allows airflow through the turbine to clear it before the next start.
False Start
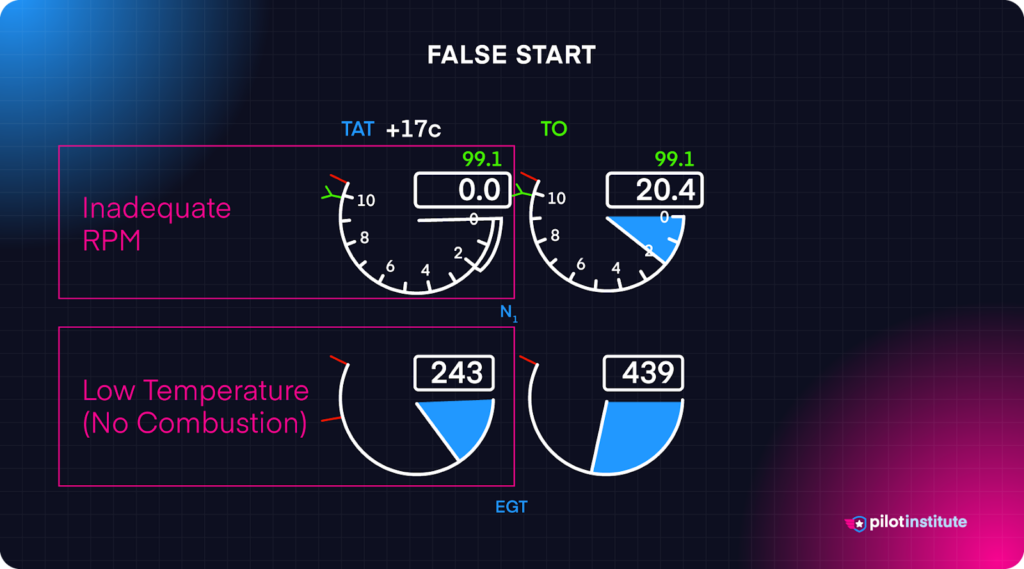
False starts occur when the starter disengages too early. This prevents the engine from reaching the necessary RPM for a successful start.
The difference between a false start and a hung start is that the engine does not achieve combustion during a false start.
When this happens, cut the fuel flow and stop the engine. You can assume there is an issue with the starter motor, so the best practice would be to contact engineers.
How Do Turbine Engines Work?
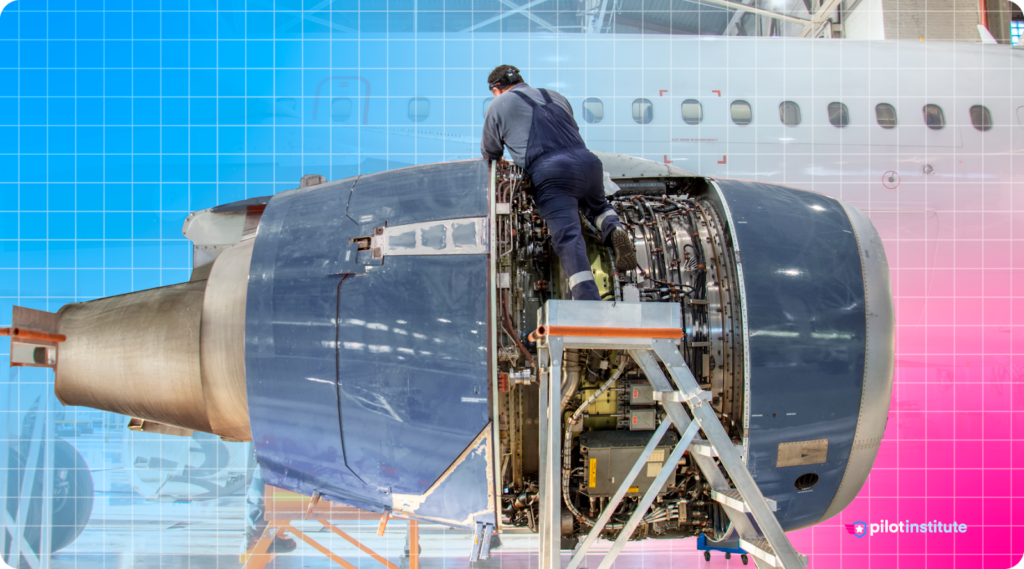
Turbine engines may be an advanced piece of engineering, but the concept is quite simple. Below, we have taken an example of a turbojet engine. It’s the most basic of all turbine engines.
We need to take a quick look at how a jet engine works to understand how it can fail to start.
The Basic Principle
A turbine engine generates thrust by compressing air and mixing it with fuel. The mixture is then ignited, creating an expanding gas. This gas drives a turbine and produces high-speed exhaust gases.
Turbine engines come in various shapes and sizes. But they all share the same fundamental components:
- Compressor Fan – This spins to increase the pressure of incoming air.
- Combustion Chamber – Where the fuel ignites to generate energy.
- Turbine – Driven by the expanding gasses from burning the fuel.
The Four Main Stages
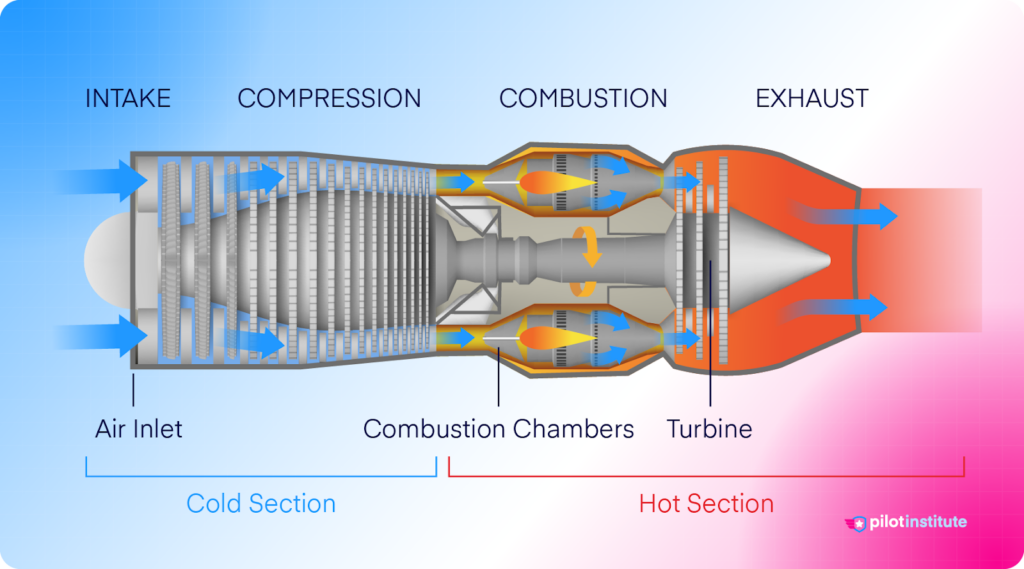
There are four main stages of a basic turbine engine:
- Air intake (Suck)
- Compression (Squeeze)
- Combustion (Bang)
- Exhaust (Blow)
The stages are split up into two sections. The cold section (intake and compression) and the hot section (combustion and exhaust). Let’s take a look at each step in a bit more detail.
Stage 1: Air Intake
The air intake’s main job is to smoothly guide air into the compressor blades. It is tube-like in shape to help direct airflow.
The air flowing into the compressor must be subsonic, which means it is slower than the speed of sound. The air intake captures and slows the air before it enters the compressor.
Stage 2: Compression
The compression stage consists of a series of compressor blades. It’s connected to and driven by the turbine.
It compresses incoming air, increasing its pressure. As air moves through the compressor, it becomes more and more compressed.
Stage 3: Combustion
The combustion section consists of the combustion chamber and the turbine. The high-pressure air mixes with fuel and ignites. As this mixture is burned, it passes through the engine towards the turbine.
The turbine absorbs the energy from the ignited mixture. This turns the compressor.
Stage 4: Exhaust
The exhaust section consists of a nozzle. The high-speed air exits the engine, producing thrust and pushing the aircraft forward.
How Does a Turbine Engine Start?
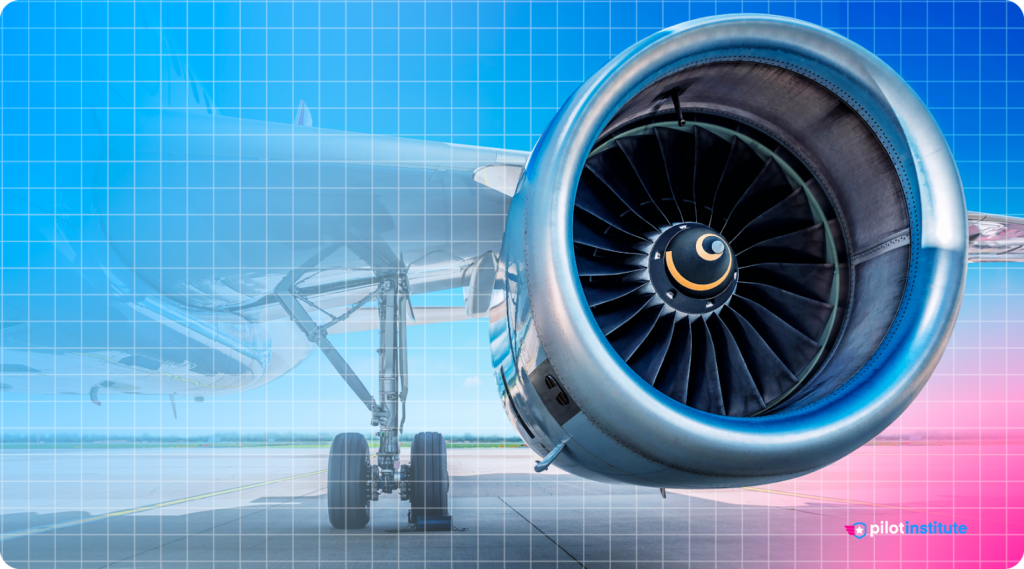
Unlike a piston engine, turbine engines run off continuous combustion. That means there is no need for constant lighting once it gets itself going.
But to start the engine, we need to get enough compressed air flowing into the combustion chamber. To do this, we must manually spin the compressor at a high enough speed.
Light off occurs once enough compressed air flows into the combustion chamber and mixes with the fuel. The turbine then becomes self-sustaining.
So, how do we get the compressor spinning fast enough to produce compressed air?
Starters.
There are many different types of starters. Let’s go over the most common.
Types of Starters
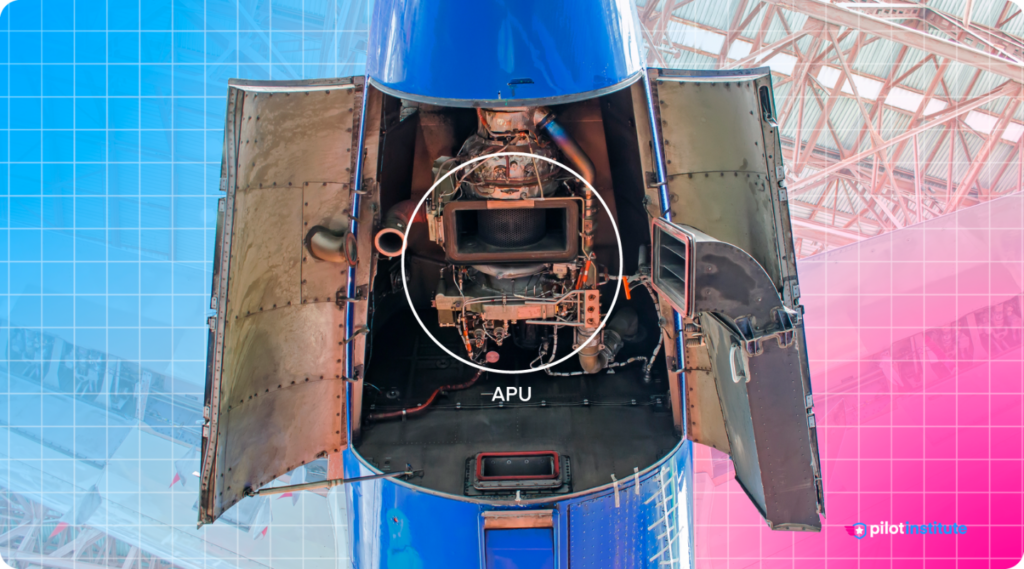
Electric Starters
Electric starters are common in smaller jets. Some aircraft have starter generators, which are starters that act as engine-driven generators once the engine is running. The starters require electricity from the aircraft, and external power units can also provide this.
Hydraulic Starters
Hydraulic starters use a geared hydraulic motor. This motor gives the initial energy required to spin the compressor.
Air Starter
An air starter uses a high flow of compressed air to speed up the compressor. This compressed air comes from the APU (Auxiliary Power Unit). You can also produce the compressed air through external gas generators.
Conclusion
In this article, we covered the turbojet engine, but what is the difference between a turbojet and a turbofan? Check out this article to find out.